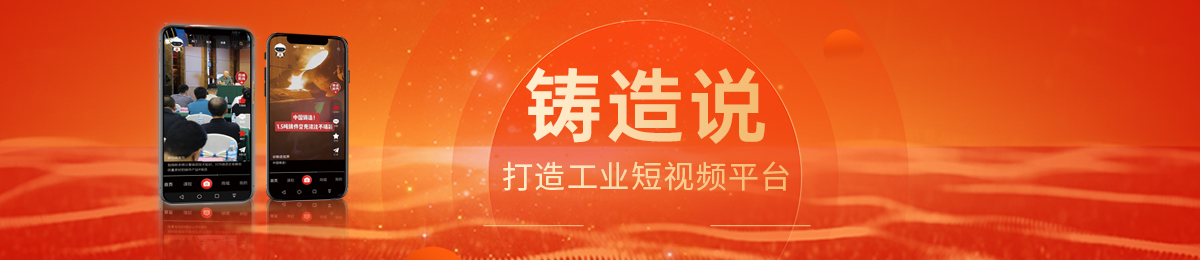
您好, 欢迎来到百铸网! 热线电话:400-8088-177 企业邮箱:[email protected] 注册|登录
2016-06-24来源:暂无数据
Chen Bing
(Beijing University of Aeronautics and Astronautics)
ABSTRACT this paper reports the investment castings dimensional tolerance standards, and describes the influence of various process parameters on the dimensions stability of castings. The author presents the assignment for the tooling allowance in the investment casting industry, and indicates the essentiality of the right measurement system .
Key World: Investment Castings, Dimensions Accuracy, Tooling Allowance
不断提高熔模铸件的尺寸精度,减少因尺寸超差造成的废品,始终是国内外熔模铸造工作者追求的主要目标之一。
一.熔模铸件尺寸稳定性
1.蜡模尺寸稳定性及其影响因素
图 1是美国宾夕法尼亚大学Robert C. Voigt教授对29种精铸件跟踪测量后所得结果[1]。可见在多数情况下蜡模尺寸波动大时铸件尺寸波动也大,例外情况是少数。从总体看蜡模的尺寸波动在铸件尺寸波动中占 10%~70%。
制模工艺参数对蜡模尺寸稳定性有决定性的影响。主要因素如下:
(1)压蜡温度
压蜡温度的影响,不同模料有不同的表现(见图2)[2]。由图2可见,采用蜡基模料时,压蜡温度对蜡模尺寸稳定性的影响很敏感,而树脂基模料则影响较小。
(2)压注压力(见图 3) [2]
由图 3 可见,压力较小时压力增大蜡模收缩率明显减小。然而压力增大到一定程度后(≥1.6MPa),压力大小对蜡模尺寸几乎没有影响。难怪国外试验结果往往得出“压力大小与蜡模尺寸无关”的结论,而国内许多企业的印象却不尽然。
(3)流动速度
可以通过以下二个途径来改变模料的流动速度,对蜡模尺寸的影响却不尽相同:
·通过改变压蜡机流动速度设定 此方法对蜡模收缩率影响较小。但对形状复杂薄壁件或带型芯的蜡模充型和表面质量却有着重要影响。
·通过改变注蜡口截面积 此方法影响较大,因为增大注蜡口截面积不仅可以降低压蜡温度,而且还可以延长注蜡口处模料的凝固时间,从而增加蜡模被压实的程度,减小收缩率和表面缩陷。
(4)压注时间
这里所谓压注时间包括充型、压实和保持等三个时间段。充型时间指模料充满压型型腔的时间;压实指充满压型至射蜡嘴关闭的时间;保持指从射蜡嘴关闭至起模的时间。
压注时间对蜡模收缩率有显著影响(图 4)[3],这是因为增加压注时间就可能有更多的模料被挤压进入型腔,蜡模被压实程度更大,从而减小收缩率。蜡模重量随压实时间延长而增加即可证明这点(见图5)[3]。压实时间长短应合适,如果压实时间过长,注蜡口处的模料已经完全凝固,压实也就不起作用了。从图4还可见,当压注时间较短时(15~25s),压蜡温度上升,收缩率增大;但当压注时间延长至 25~35s(在充填时间保持恒定的前提下,实际上是延长了压实时间)压蜡温度的影响变小;当压注时间增加到 35s以上,还会出现相反的情况,即随着压蜡温度上升,蜡模收缩率反而会变小(见图 5)。此现象可以解释为,提高模料温度和延长压实时间一样都有增加蜡模压实程度的作用。
(5) 压型温度和压蜡设备
压型温度高,蜡模冷却慢,收缩率增大。这是因为起模前蜡模还在压型中,收缩受限制,而起模后则变为自由收缩。所以如果起模时蜡模温度高则最终的收缩率大,反之则收缩率小。
同理,压蜡机的冷却系统对蜡模尺寸可能产生大约0.3%的影响。
最后值得强调指出的是,采用蜡基模料时,蜡膏是一种固、液、气三相共存体系。三相之间的体积比,对蜡模尺寸影响颇大。而这三者之间的比例关系在实际生产中无法控制,这也是采用蜡基模料压制蜡模尺寸稳定性较差的重要原因。
2. 型壳材料和制壳工艺对铸件尺寸稳定性的影响
型壳对铸件尺寸的影响主要是由于型壳焙烧时的热膨胀、热变形(高温蠕变)和型壳对铸件冷却收缩的约束(阻碍)等因素引起的。
(1) 型壳热膨胀
主要取决于型壳材料。 不同耐火材料膨胀率不同。常用耐火材料中以熔融石英膨胀率最小,硅酸铝次之,硅石最大且不均匀。经试验确定硅酸铝型壳从室温加热至 1000℃,型壳可产生大约0.25%的膨胀,在铸件尺寸综合收缩率中所占比例并不大,所以,如果采用此类耐火材料,型壳具有较好的尺寸稳定性, 如采用熔融石英无疑会更好。但如果采用硅石,型壳尺寸波动就很大。
(2) 热变形(高温蠕变)
例如以水玻璃为粘结剂的型壳,在 1000℃以上高温蠕变程度明显大于硅溶胶和硅酸乙酯型壳。而电熔刚玉本身虽然耐火度较高,但由于往往存在氧化钠等杂质,所以型壳焙烧温度高于 1000℃也可能产生蠕变,致使尺寸稳定性欠佳。
(3) 型壳对铸件收缩的约束——型壳的退让性和溃散性 这也主要取决于型壳材料。
综上所述,型壳对铸件尺寸波动的影响, 耐火材料起主要作用,然而粘结剂的作用也不容忽视。相比之下,制壳工艺的影响较小。
3. 铸件冷却不均产生应力对尺寸稳定性的影响
铸件(包括浇注系统)各部分冷却快慢不同而产生热应力使铸件变形,进而影响尺寸稳定性。这在实际生产中也是经常遇到的。降低铸件冷却速度和改进浇道组合方式都是行之有效的预防措施。
二. 提高准确度的关键——模具收缩率赋值正确
以上所说的“尺寸稳定性”跟“尺寸准确度”、“精确度(精度)”是有区别的。尺寸稳定性(即精密度)跟尺寸一致性是同义的,反映尺寸波动或分散的程度,通常以标准差σ来衡量。尺寸不稳定的原因主要是工艺控制不严,它属于随机误差。准确度则是指对铸件上某个尺寸而言,众多测量值的算术平均值偏离名义尺寸的程度, 即平均偏差的大小。对熔模铸造来说,尺寸准确度差的原因主要是压型设计时收缩率赋值不当,是一个系统误差,通常通过反复返修模具来调整。而尺寸精确度(精度)则是上述二者的综合。所以要提高铸件尺寸精度,解决产品尺寸超差问题,不但要严格控制工艺过程,减小尺寸波动,同时还要在设计压型时对铸件每个尺寸的收缩率正确赋值。
众所周知精铸件最终的总收缩率是蜡模、合金收缩和少量的型壳膨胀综合而成。其中型壳膨胀约 0.25%,所起作用有限。尽管合金的线收缩率往往比蜡模大,但压蜡过程造成的尺寸波动却影响更大。为了减少模具返修费用和减小铸件尺寸波动,控制好蜡模收缩率至关重要。
1. 蜡模收缩率
测量蜡模收缩应在蜡模尺寸完全稳定下来之后进行。这是因为起模后蜡模收缩往往并未完全停止,蜡模尺寸有时在起模几天后才最终稳定下来,但多数模料的收缩是在起模后一至数小时内基本完成。蜡模收缩率主要有以下影响因素:
(1) 模料种类;
(2) 蜡模断面尺寸;
值得强调指出的是蜡模断面尺寸对收缩率有显著影响(图 6)。表 1 所示为某种典型的无填料模料在压制不同厚度蜡模时的收缩率。蜡模的断面厚度一般不应超过13mm。厚度大于13mm时可通过使用冷蜡块或金属型芯来减小壁厚,从而达到减小收缩的目的,这对于无填料模料特别重要[4]。
表 1 典型无填料模料蜡模的收缩率 (%)
自由收缩 |
限制收缩 |
|
厚断面(>13mm) |
1.00~2.00 |
0.75~1.25 |
正常断面(3~13mm) |
0.50~1.00 |
0.50~0.75 |
薄断面(<3mm) |
< 0.75 |
< 0.5 |
注:1. 水溶性模料收缩率约为0.25%;
2.当使用可溶芯、陶瓷芯、石英玻璃管时,蜡模上与型芯接触部分没有线收缩;
(3) 型芯种类
蜡模内腔尺寸无疑是与型芯外形尺寸保持一致的。因此采用型芯便成为提高蜡模内腔尺寸精度的一种方法。
2. 合金收缩
合金收缩主要取决于以下一些因素:
· 铸造合金种类和化学成分;
· 铸件几何形状(包括约束状态和断面尺寸);
· 铸造参数,例如浇注温度、型壳温度、铸件冷却速度等;
· 陶瓷型芯、石英玻璃管等的使用。
由于浇注温度、型壳温度、铸件冷却速度等工艺参数在生产过程中一般都要通过标准工艺卡严格加以控制,所以不同生产批次之间,由此引起的尺寸波动并不大。即使浇注温度超出工艺规程要求的范围,铸件尺寸波动通常也不大(见表 2) [4]。跟蜡模相似,铸件断面尺寸和型壳的约束才是影响合金收缩的主要因素。经验表明,全约束尺寸收缩率为自由收缩率的 85%~89%;半约束尺寸为94%~95%。表3列出常用合金铸件的收缩率(不含蜡模收缩率)[4]。
表 2 CF8M 精铸件收缩率随浇注温度的变化
试样尺寸编号 |
浇注温度/℃ |
型壳+铸件的综合收缩率 (6 个试样平均值,%) |
I (实心) |
1538 |
2.1 |
1 (实心) |
1566 |
2.0 |
1 (实心) |
1593 |
2.2 |
1 (实心) |
1649 |
2.1 |
1(空心) |
1538 |
1.9 |
1(空心) |
1566 |
1.8 |
1(空心) |
1593 |
1.9 |
1(空心) |
1649 |
1.8 |
注:型壳温度 982℃
表 3 铸件收缩率(不含蜡模率) %
合金种类 |
约束尺寸收缩 |
薄断面尺寸 (≤9.5mm) |
厚断面尺寸(>9.5mm) |
碳钢和合金结构钢 |
1.50 |
1.8 |
1.90 |
400 系列不锈钢 |
1.80 |
2.00 |
2.20 |
300 系列不锈钢或相当的 国外牌号以及钨铬钴合金 |
2.0 |
2.3 |
2.6 |
铜合金 |
1.80 |
2.0 |
2.2 |
铝合金 |
1.0 |
1.2 |
1.4 |
注:型芯周围尺寸收缩率 0.25%~1.0%
3. 首批供测量用样件的最少数目
以上所列收缩率是建立在以往经验基础上的经验数据,并非真实的收缩率。按照这些数据设计制造模具,返修在所难免。为了提高返修的准确程度和成功率,减少返修次数,一个关键环节是认真检测数量足够的试铸样件的尺寸。因为我们生产的铸件尺寸不可能完全一致,所以只有测量样件数量足够多,得出的平均值才能接近真正的算术平均值。由此不难看出,测量样件的最少数目跟生产工艺控制产品尺寸一致性的能力(Process Capability )有直接关系,如果铸出的铸件尺寸完全一致,那么只需检测一个样件就够了;反之,如果铸出的铸件尺寸波动很大,
就要测量很多样件才能得出较为准确的收缩率数据。前已提及,生产工艺控制尺寸的能力可用此种工艺生产出铸件尺寸的 6σ来代表。按统计学原理算出检测样件的最小数目如表 4 所列[5]。
表中 Hp 指生产工艺控制尺寸的能力 P6σ与相应尺寸公差值 TC之比,即Hp=P6σ/TC。按表 4,Hp 越小,即生产工艺控制尺寸的能力强而尺寸公差要求又松,则要求首批检测的样件数就可以越少;反之Hp越大,则要求检测的样件数目就越多。例如 (Hp<0.1), 只要检测一个样件即可;如果Hp >0.6,则需要检测的样件数目至少是44个。从目前多数熔模铸造厂的工艺技术水平看,Hp大多在0.5 以上,所以首批测量样件一般至少需要 11个。
表 4 首批检测样件的最少数目
Hp |
测量样件的最小数目/ 个 |
<0.1 |
1 |
0.1~0.2 |
2 |
0.2 ~ 0.3 |
2 |
0.3 ~ 0.4 |
3 |
0.4 ~ 0.5 |
5 |
0.5 ~ 0.6 |
11 |
0.6 ~ 0.7 |
44 |
0.7 ~ 0.8 |
44 |
0.8 ~ 0.9 |
44 |
0.9~1.0 |
44 |
>1.0 |
44 |
三. 测量系统分析
在分析和解决产品尺寸问题的时候,必须注意到所采用的测量系统的精度和可靠性。除测量仪器设备本身必须经常校准外,尽量减少测量误差也很重要。如果测量系统(包括操作人员和操作方法)误差较大,不但可能将废品判为合格品,也可能将许多合格品误判为废品,二者均可能造成重大事故或不必要的经济损失。判断测量系统对某一特定测量任务是否适合,最简单方法是进行再现性(reproducibility) 和重复性(repeatability)鉴定试验。所谓重复性是指同一检验员用同一仪器(或设备)和方法检查同一零件,获得结果的一致性。再现性指不同操作者使用不同仪器检查同一零件,获得结果的一致性。美国汽车工业活动组( Automotive Industry Action Group)规定以重复性和再现性综合标准差R&R在被测量铸件尺寸波动标准差中所占百分比≤30%作为测量系统满足要求的标准[5]。在测量某些尺寸较大而形状复杂的铸件,并非所有测量系统都能达到此要求。而测量模具时允许的测量误差还应更小,通常为其1/3。
表5中列出了美国若干精铸厂常用的测量仪器设备的再现性、重复性和R&R误差实况调查统计[5]。由表5 可见同类仪器,测量误差大小之间相差甚远,说明铸造厂中许多检测系统(包括测量仪器设备、操作人员和测量方法)不符合要求。大的再现性误差常常是因使用不适当的仪器设备或操作方法不合理造成的。而重复性误差大则往往是操作者的技术不佳所致。
表5 几种常用测量仪器设备测量误差比较
仪器种类 |
再现性误差 /mm |
重复性误差 /mm |
综合误差 R&R /mm |
||||||
平均值 |
最好 |
最差 |
平均值 |
最好 |
最差 |
平均值 |
最好 |
最差 |
|
数显卡尺 |
0.320 |
0.046 |
1.509 |
0.159 |
< 0.005 |
0.473 |
0.382 |
0.062 |
1.509 |
测微千分尺 |
0.124 |
0.028 |
0.474 |
0.152 |
< 0.005 |
0.267 |
0.208 |
0.061 |
0.838 |
划线机 |
0.202 |
0.008 |
0.840 |
0.0203 |
0.005 |
0.0355 |
0.4572 |
0.1803 |
1.021 |
三坐标测量机 |
0.030 |
0.002 |
0.137 |
0.009 |
< 0.003 |
0.041 |
0.035 |
0.002 |
0.137 |
四.模具结构和加工水平
众所周知模具结构和加工质量对蜡模尺寸和几何形状均有重要影响。例如定位、夹紧机构是否准确可靠,活动部分(如活块、插销等)的配合间隙是否恰当,起模方式是否对有利于保证铸件尺寸精度等。无庸讳言,对于目前国内相当多数的精铸厂来说,模具设计和制造水平仍急待提高。
五.结论
由上述分析不难看出,提高熔模铸件尺寸精度是一个系统工程,涉及精铸生产过程的方方面面。其中要点可概括如下:
1) 严格控制制模工艺参数,特别是对铸件尺寸有显著影响的参数。
2) 选择适当的型壳材料。
3) 以符合统计学原理的正确方法收集、统计和分析有关收缩率的数据,提高收缩率赋值的准确性。
4) 经常监察测量系统(包括仪器设备、检验人员和技术),使重复性、再现性误差达到规定要求。
5) 不断提高模具设计和制造水平。
6) 在许多场合铸件矫正和稳定化热处理等措施仍然不可或缺。
友情链接 友链交换添加QQ:2694467624 其他问题请咨询网站客服