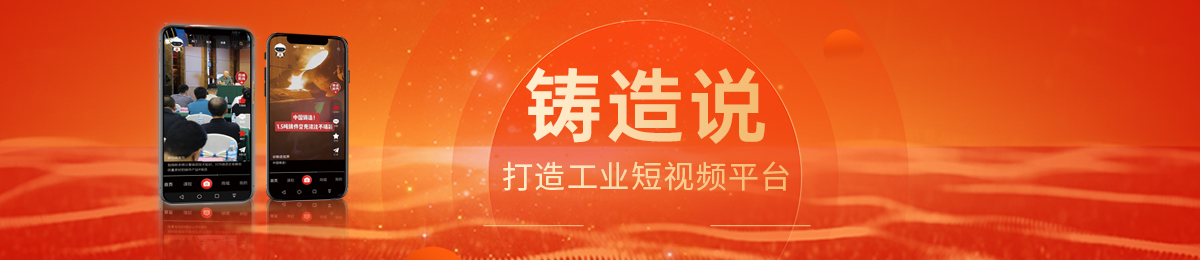
您好, 欢迎来到百铸网! 热线电话:400-8088-177 企业邮箱:[email protected] 注册|登录
2016-06-20来源:暂无数据
由于生产条件及环境的变化,必然导致铸件其他参数发生变化,如果不能及时调整型
砂工艺,砂系统将会呈现不稳定状态,最终导致铸件清理难度加大甚至于报废;这样,就
需要调整原有的型砂工艺稳定砂系统;型砂的材料构成主要是由旧砂、原砂、膨润土和添
加剂等组成。由于型砂 95%以上是旧砂,而旧砂由于浇注铸件的砂铁比不同、芯砂混入量
不同等因素的影响,导致材料构成的波动非常大。因而要控制型砂的构成,就必须对型砂
中的有效膨润土含量、有效添加剂含量及含泥量进行检验,以便确定混砂时膨润土、添加
剂和原砂的补加量【1】。本文将简要介绍,笔者所在公司的铸造厂在实际生产过程中如何根
据参数的变化,调整型砂工艺以保证砂系统的稳定。
二、型砂关键参数定义:
1、有效膨润土量:有效膨润土(活性)含量的测定是根据膨润土中所含蒙脱石矿物能
吸附亚甲基蓝等染料的特性检测;是指 5.00g 型砂用 0.20%浓度试剂纯亚甲基蓝溶液的滴
定量[mL];再根据膨润土的标准曲线公式换算所得(%)
2、有效添加剂量:是根据型砂添加剂的发气量作对比,使用公式换算所得;即 1.00g
型砂在 900℃的发气量[mL]减去型砂中活性膨润土的发气量(计算前测得平均量)再与 1g
添加剂发气量对比(%)。
3、含泥量:国标 GB/T9442-1998 中规定直径小于 20μm 的微粉颗粒为泥份。通常使用冲洗法将泥份去除【2】。
4、型砂粒度:以 AFS 细度表示,即根据假想的筛号问接地反映砂粒的平均尺寸【3】;
5、AFS 细度的计算方法:美国铸造师学会规定的 AFS 细度的测定步骤
和计算方法如下:
①.先称取待测定的砂样 50g 左右,洗去泥分、烘干,再进行筛分
②.称量并纪录各筛上停留的砂粒的质量;
③.计算各筛上停留的砂粒量占砂样总量的百分数;
④.将各筛上停留的砂粒量的百分数乘以与各筛对应的“AFS 细度乘数”;
⑤.将以上就各筛号求得的乘积相加,求得总和:
⑥.将第 5 项求得的总和,除以第 3 项各筛上停留砂量的百分数的总和,即得到 AFS
细度
三、调整方案:
该厂使用的混砂设备为 DISA 碾砂机,造型设备 KW 静压造型线;利用半年时间的数据统计,对其型砂系统制定了如下方案:
1、数据统计:
① 根据造型主机设定值确定每箱型砂加入量,根据每箱铸件及浇注系统重量,铸件所使
用芯砂量统计每箱铸件的砂铁比;
② 统计废砂排废量及芯砂、辅料使用量统计
③ 型砂系统的除尘量统计
2、型砂调整:
① 根据生产情况,当某一铸件连续生产两天或两天以上时,将型砂辅料(膨润土、添加
剂)的加入量固定,统计型砂有效量的变化情况,然后陆续在其他铸件连续生产时逐步验
证砂铁比与加入量的关系;
② 型砂粒度调整:根据 50/100 筛号的中值调整(50/100 筛号的硅砂,其平均细度的中
值为 50【4】),当型砂的 AFS≤50 时,通过加入细砂 70/140 或更细的新砂 140/70 调整,
每碾加入 30kg-60kg,分析粒度变化情况。 ③ 型砂含泥量调整:通过对每天除尘量的统计,分析型砂系统含泥量的变化情况;
四、具体调整过程:
1、 铸件砂铁比统计:
(注:由于 X2B1 缸体为整体砂芯成型浇注,对型砂无烧损,因此铸件对外型砂的重量按“0”计算)
2、 根据铸件的砂铁比调整有效量,56D 缸体的砂铁比 6.57,在以上铸件中属于缸体类铸
件中砂铁比为最高的一种,因此首先以 56D 缸体进行试验:
在连续三天生产 56D 时,添加剂的加入量 22kg/碾,粘土加入量 33kg/碾;添加剂的有
效量由 4.55%升到 5.03%;粘土有效量由 6.56%升到 7%;约增加了 0.5%;说明生产 56D 缸
体时,按此加入量调整高于砂系统的平衡值;
通过以上的数据分析,辅料加入量作出如下调整:
1)再生产该缸体时,添加剂的加入量调整到 19kg/碾,粘土加入量 26kg/碾时,连续三天的数据统计发现,添加剂的有效量由 4.36%变为 4.29%;粘土有效量由 7.22%变为 7.11%;
有效量波动 0.1%; 因此,该工艺调整方案合理,可保证型砂系统平衡;
2)同理通过试验数据分析及理论推算其他铸件的辅料加入量与有效量的关系;再生产不同铸件时,调整合适的辅料加入量。
3、分别使用 70/140 目新砂及 140/70 新砂调整型砂粒度(原型砂的含泥量 11.42%):
① 1 月 16 日-1 月 21 日,五天共碾砂 4257 次,约循环 4257*3/900=14 次;每循环一圈的粒度约变化 0.26(每碾); 因此 1 月 16 日型砂 AFS 值 49.15;从 1 月 16 日开始连续加入五天 70/140 的新砂调整粒度,每碾加入 60kg,1 月 21 日型砂 AFS 值为 52.84;
② 1 月 25-1 月 27 日,三天共碾砂 2165 次,约循环 2165*3/900=7 次;每循环一圈的粒度约变化 0.22(每碾); 因此,1 月 24 型砂 AFS=52.44,当型砂粒度达到 52-53 时,继续加入 70/140 的新砂对砂系统 AFS 的影响很小;从 1 月 26 开始连续加入三天 140/70 的新砂调整,每碾加入60kg,1 月 28 型砂的 AFS=54。
(注:①一汽企业标准规定 70/140 石英砂 70,100,140 过筛率≥80%,其中 70,100 过筛率
≥60%;140/70 石英砂 70,100,140 过筛率≥80%,其中 100,140 过筛率≥60%;
②每碾碾砂量 3 吨,系统砂量估算 900 吨)
4、连续三个月含泥量与除尘量的对比情况:
2~3 月由于北方气候寒冷,冷的除尘管道在抽走热的粉尘后,管道内的粉尘遇冷凝
固,如果管道清理不及时,堵塞现象频出,每天排放量 4~8 吨不等,砂系统的含泥量波动
较大,在此期间,只有通过增加除尘设备的风量及疏通管道,提高其除尘能力,降低含泥
量;
进入 4 月份后,温度逐渐升高,粉尘遇冷凝固现象不再出现,除尘量逐渐趋于稳定,
达到每天 7-8 吨平均排放,含泥量波动范围缩小;
降低型砂系统含泥量还可通过加新砂或降低辅料加入量,在试验结论中将阐述该两种
方法的弊端。
五、试验结论
1、 型砂辅料有效量调整
膨润土晶体受热造成一定程度破坏,再加水混合后湿态黏结力将明显下降。更高温度
和更长时间加热后,膨润土的晶体结构完全破坏,就变成没有黏结力的“死黏土”。铸件
厚度增大,砂铁比低,浇注温度高和冷却时间长都都使膨润土的烧损量增多。
判断型砂中有效煤粉是否足够的最直接方法是观察铸件表面的光洁程度和有无粘砂。
受到浇入金属液热作用,旧砂中一部分煤被烧损,需要补充。另一方面,新加入材料如新
砂、混入芯砂和膨润土也需要靠加入煤粉使达到有效煤粉量的水平。混砂时煤粉总加入量
是烧损量与额外补充量之总和【5】。(有效煤粉即相当于文中的有效添加剂)
2、型砂粒度的调整:
高压造型的型砂粒度一般为 50/140,而树脂砂芯粒度大多是 50/100 或更粗些。芯砂
混入量过多就会影响整个湿型旧砂的粒度变粗,从而引起型砂透气性增高,铸件表面变得
粗糙。为了保持型砂的粒度不致变粗,可将除尘系统的微粒回收到旧砂中。或是加入细粒
新砂来调整;如文中所提的铸造厂,当型砂的 AFS 达到 48 左右时,通过连续加入 70/140
或 140/70 的新砂调整;但是,由于铸件溃散入砂系统的芯砂量已经很大,如果型砂粒度不
是粗化到难以承受的程度,新砂不建议如此连续大量的加入,否则会由于新砂量过大对型
砂系统的其他性能指标(含泥量,有效量以及强度)带来影响;
3、含泥量的调整
含泥量的升高,会导致型砂透气性下降,浇注过程中会产生“气爆”现象,铸件就会
因爆炸粘砂报废。型砂系统的含泥量不能过高;降低砂系统的含泥量可通过降低辅料加入
量,但是有效膨润土量的降低会导致型砂强度下降,起型能力以及抗夹砂能力降低;有效
添加剂量的降低会导致型砂的抗粘砂能力下降。
如果增加新砂的加入量调整含泥量,首先计算出各种新加入材料在浇注后的型砂中产
生多少泥分,才能计算出这些泥分需要加入多少原砂才能够使型砂含泥量符合工艺规定。
如文中所提的铸造厂每碾加 30 公斤的新砂,含泥量可降低 0.1%;但是新砂加入量过多,
不但造成成本的浪费而且还会使型砂系统旧砂比例下降将使型砂性能降低,型砂发散,影
响型砂的起模能力,砂型在浇注过程中出现冲砂现象;
因此,笔者认为如果能通过调整除尘设备控制砂系统的含泥量才是最佳选择。
总而言之,稳定型砂系统就是为了能够生产出品质优良的铸件。通过这一理念我们要
不断的根据变化的生产条件调整型砂工艺,以满足生产需求。
友情链接 友链交换添加QQ:2694467624 其他问题请咨询网站客服